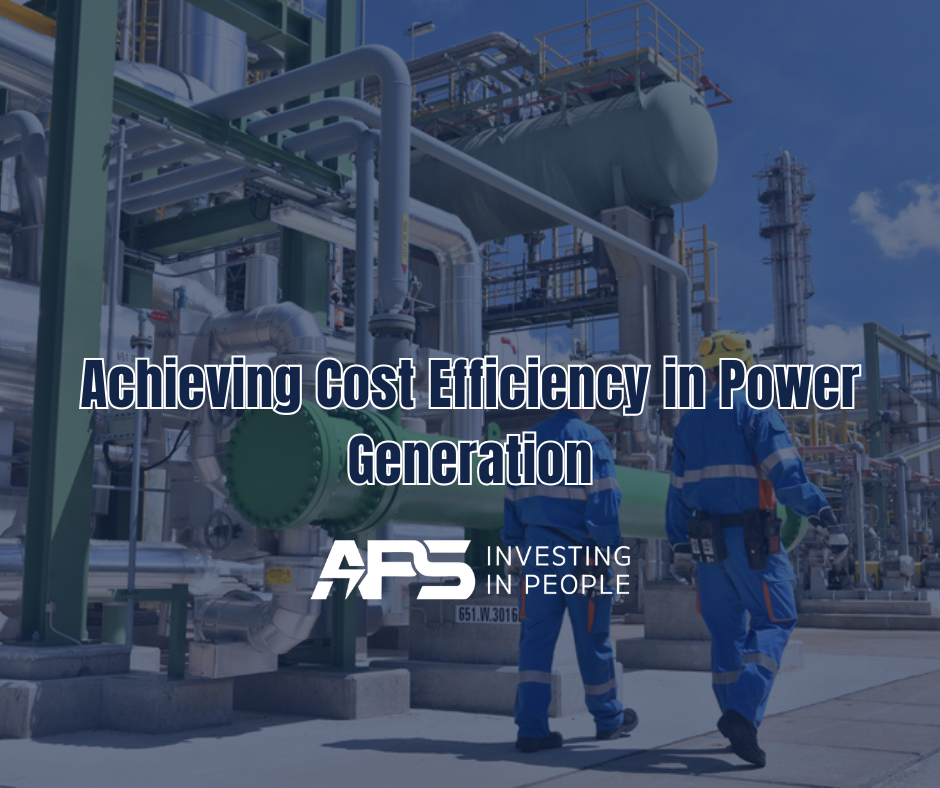
The power generation industry is at a critical juncture, facing the dual challenges of increasing energy demand and a widening skills gap. In this landscape, retaining skilled workers has become paramount for maintaining operational continuity and cost efficiency. High turnover rates not only disrupt operations and compromise safety and reliability but also significantly inflate costs, undermining the industry’s economic viability. Power plant executives, energy sector leaders, and HR managers are thus tasked with the crucial challenge of devising cost-efficient strategies that keep skilled employees engaged and committed to their roles.
This blog delves into the multifaceted factors driving turnover in the power generation sector and presents a suite of actionable, cost-effective retention strategies. By exploring approaches ranging from competitive compensation packages to enhanced work-life balance initiatives and recognition programs, we aim to provide a comprehensive roadmap for ensuring a motivated, skilled, and loyal workforce. These strategies are designed not only to address immediate retention concerns but also to foster long-term cost efficiency by reducing the financial burden of frequent hiring and training cycles. By implementing these practices, power generation companies can create a stable, productive workforce that drives operational excellence while maintaining fiscal responsibility in an increasingly competitive energy landscape.
Understanding the Challenge: Why Employees Leave
Employee retention in the power generation industry is fraught with challenges. According to recent industry insights, many skilled professionals leave for the following reasons:
- Aging Workforce: The energy sector is heavily impacted by an aging workforce nearing retirement without adequate replacements.
- Lack of Career Growth: Employees often leave due to limited opportunities for advancement or skill development.
- Burnout and Poor Work-Life Balance: Given the demanding nature of the industry, employees may experience burnout if their well-being isn’t prioritized.
- Competitive Job Market: The demand for power sector professionals has outpaced supply, leading employees to seek opportunities offering higher pay or improved conditions, which can impact cost efficiency if not managed properly.
Power plant Longevity & Cost Efficiency
Different types of power plants have varying operational lifespans:
Nuclear Power Plants
- Initially designed for 40-year lifespans
- Many have received 20-year extensions, allowing operation up to 60 years
- Some are now applying for additional extensions to operate for up to 80 years
- The average age of operating U.S. reactors is approaching 40 years
Coal-Fired Power Plants
- Historically, coal plants have retired at an average lifetime of 46 years globally
- Many can operate for 50-60 years or longer
- Achieving climate goals may require reducing operational lifetimes to 35 years
Solar Power Plants
- Typical lifespan of 25 to 30 years, but many can operate longer
- Industry now projecting lifespans of 35 to 40 years for newer solar farms
- The estimated operational lifespan of a PV module is about 30-35 years
Wind Turbines
- Average lifespan of 20 to 30 years
- As of 2025, many wind turbines worldwide are approaching retirement
The extended lifespans of power plants, ranging from 20-30 years for wind turbines to up to 80 years for nuclear reactors, emphasize the critical importance of long-term workforce planning and retention strategies.
Enhancing Cost Efficiency
Competitive Compensation and Benefits
While offering competitive salaries is important, it’s equally crucial to provide a comprehensive benefits package:
- Regularly benchmark salaries against industry standards
- Offer customized benefits such as flexible healthcare packages and retirement plans
- Implement retention bonuses tied to tenure or performance metrics
Transparent Communication
Open communication builds trust and fosters a collaborative environment:
- Hold regular town hall meetings or circulate newsletters to keep employees informed about plant operations and future plans
- Create two-way feedback channels for employees to voice their thoughts
- Ensure clarity around role expectations and their impact on long-term plant objectives
While these strategies may seem costly at first glance, there’s a cost-effective solution that can help power plants implement them without overextending their budgets: partnering with a staffing company that specializes in staff augmentation for the power generation industry.
Staff Augmentation as a Cost-Effective Solution
Staff augmentation can be an effective strategy for managing workforce needs throughout a power plant’s life cycle while maintaining cost efficiency:
- Flexible Workforce Scaling: Augment your team during peak periods or for specific projects without the long-term financial commitment of full-time hires.
- Access to Specialized Skills: Quickly bring in experts for emerging technologies or specific plant types without the expense of full-time recruitment and training.
- Cost Control: Reduce overhead costs associated with full-time employees while maintaining productivity and operational efficiency.
- Knowledge Transfer: Use augmented staff to train and upskill your permanent workforce, ensuring knowledge continuity without the expense of external training programs.
- Reduced Recruitment Costs: Leverage the staffing company’s expertise and networks to find qualified candidates quickly and cost-effectively.
- Risk Mitigation: Staffing companies often handle payroll, benefits, and other administrative tasks, reducing your HR overhead and compliance risks.
- Improved Work-Life Balance: Use augmented staff to cover shifts or projects, allowing your full-time employees more flexibility and reducing burnout.
By strategically utilizing staff augmentation, power plants can implement robust retention strategies while optimizing cost efficiency. This approach allows you to invest in your core team’s development and well-being, ultimately fostering a more stable, skilled, and loyal workforce capable of supporting your plant’s operations throughout its extended lifespan in a cost-efficient manner.
Contact APS Solutions now to learn how we can tailor our staff augmentation services to your unique needs and help secure your plant’s future for decades to come.